الوار و کنده درخت
هنوز هم برخی کارخانه های تولید پارکت چوبی مهندسی، تولید خود را با تنه درختان آغاز میکنند، که در نهایت به ونیر “پوسته ای” یا “چرخشی” تبدیل میشوند. قبل از خرید، انتهای کنده ها اندازه گیری شده تا قیمت آنها مشخص شود. سپس آنها را علامت گذاری و وزن میکنند و قبل از اینکه به ابعاد مشخص بریده شوند در برش چیده میشوند.
اگر قرار نیست کنده ها فوراً استفاده شوند، با روشهای متفاوتی انبار میشوند. صرف نظر از این، مهمترین بخش ذخیره سازی خیس ماندن کنده هاست، چه با قرار دادن در حوضچه های آب در کارخانه، چه با پاشیدن آب روی کنده ها در فضای باز.
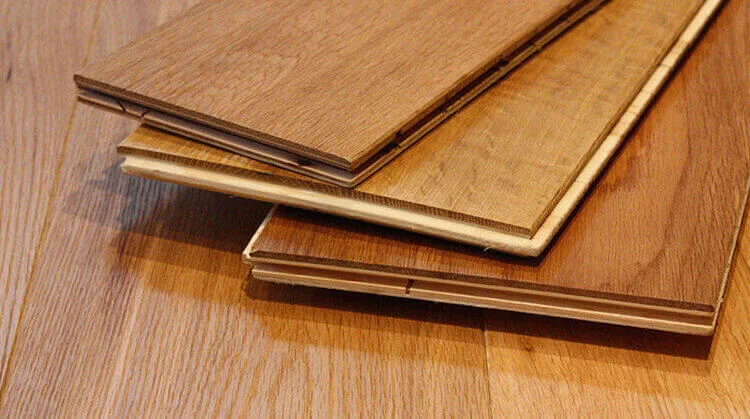
انبار چوب
بسته به برش، زمان سپری شده در دیگ بخار از یک روز تا چند هفته متغیر است. پس از آن، کنده ها به سمت پایین نوار نقاله حرکت میکنند تا دوباره به طول بریده شوند و پس از آن به سمت ماشین تراش حرکت میکنند. این دستگاه در هر سمت از دوکهایی برای برداشتن کنده ها استفاده میکند. کنده یکبار چرخانده میشود. در طی این چرخش توسط لیزری برآورد میکنند که چند دور چرخش نیاز است تا کنده گرد شود. سپس کنده چرخان به صورت گرد بریده میشود و تیغه برش کنده را به قطعات بلند از ونیر نازک تبدیل میکند.
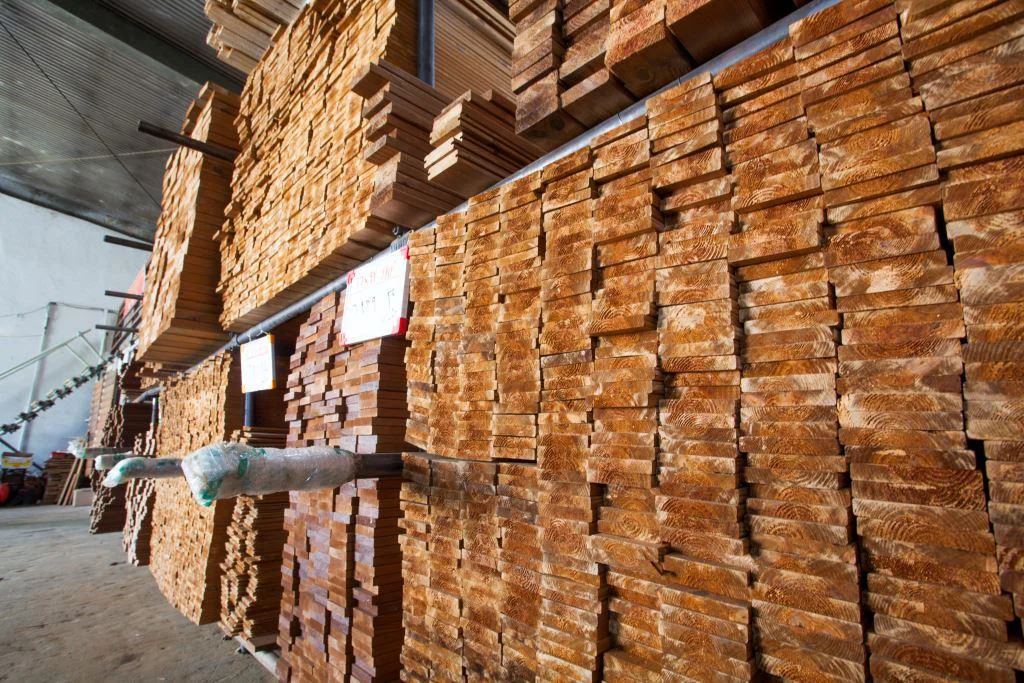
ماشین های پارکت سازی
در مرحله بعد، روکش همچنان خیس است و از نوار نقاله گذشته و از زیر چشم الکترونیکی عبور میکند که نقاط خالی و تیره روی ونیر را میخواند. ابزاری مخصوص این نواحی را میتراشد و اصلاح میکند. اکنون کیفیت ونیر به حداکثر رسیده است. سپس لاییها به عرضهای خاص برش میخورند. البته همه این مراحل با سرعت بسیار بالا انجام میشود.
سپس ورقهای لایی با انتقال توسط جرثقیل به خشک کن روی هم انبار میشوند. در این مرحله، ورق ها تخلیه میشوند و در معرض ترکیبی از هوای گرم – حدود 300 درجه – و بخار قرار میگیرند. بخار به آرامی کم میشود و در نتیجه روکشها با کمترین آسیب ممکن خشک میشوند. لایی با رطوبت 30 تا 60 درصد وارد خشک کن چوب شده، و با رطوبت 6 تا 8 درصد از آن خارج میشود و چندین سانت از ابعاد قبلی خود کوچکتر میشود. برای کیفیت محصول حیاتی است که میزان رطوبت تمام لایه ها در سطوح قابل قبول و ثابتی باشد.
اکنون لاییها آماده مونتاژ هستند. تعداد لایه ها در محصول نهایی پارکت تعیین میکند که چند ونیر به هم چسبانده شده اند. هر ونیر قبل از چسباندن 90 درجه چرخانده میشود به طوری که نقش رگه چوب در جهت مخالف قبلی قرار گیرد و به این طریق ثبات اندازه ای محصول نهایی افزایش یابد. برخی از تولیدکنندگان پارکت مهندسی شده از چوب نرم یا گونه های ارزانتر چوب سخت برای لایه های زیری پارکت استفاده میکنند و از ونیر چوب سخت فقط برای لایه فوقانی استفاده میکنند، در حالی که برخی دیگر از چوب سخت در تمام بخشهای کار استفاده میکنند.
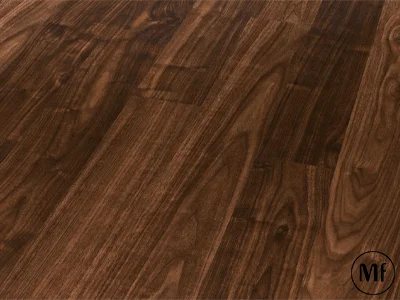
مراحل ساخت پارکت مهندسی
میز کار و قطعات پارکت روی آن
در این مرحله، چسب کاملاً مرطوب است – چسبندگی زیادی ایجاد نمیشود. پنلها به دستگاه پرس بخار فرستاده میشوند، در این مرحله چسب «عمل میکند» یا سفت میشود. برخی از شرکتها این مرحله را با یک فشار مجدد و ناگهانی انجام میدهند، که نهایتاً فرآیند چسب آغاز و زمان پرس بخار تسریع میشود.
اکنون پنلها یک سری از بررسیهای کنترل کیفیت را میگذرانند. قطعات به صورت تصادفی بریده میشوند تا بررسی شود که آیا چسب به خوبی پخش شده و به درستی چسبیده است یا خیر. صافی، ضخامت و محتوای رطوبت نیز برای حفظ دقت کنترل میشود.
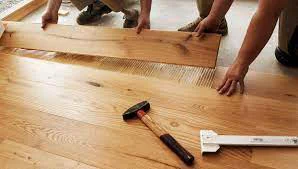
برای محصولات پارکت با طول زیاد، فرآیند مونتاژ تا حدودی متفاوت است، زیرا هر قطعه شبیه چند ردیف پارکت است. برای لایه فوقانی، بلوکهای کوچک به صورت اسلت بریده میشوند. سپس اسلتها به ضخامت و طول لازم برای الگوی مد نظر بریده میشوند. ترتیب مونتاژ قطعات بسته به سازنده قابل تغییر است. برخی از تولیدکنندگان الگو را با فشار دادن هر اسلت به پنلهای لمینت متقاطع مونتاژ میکنند. برخی دیگر از فرآیندی استفاده میکنند که اسلتهای بالایی را به یکدیگر و سپس به پنلها می چسباند.
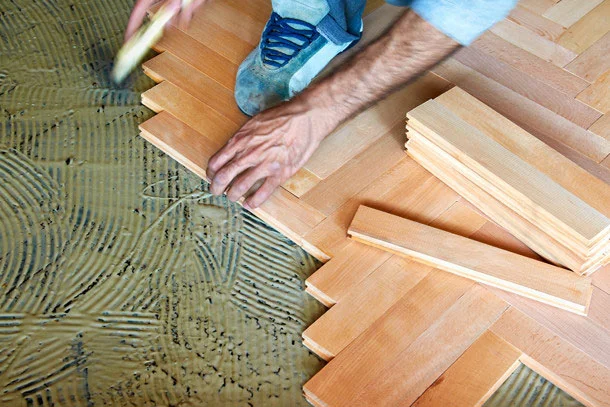
مرحله بعدی، چه برای پارکت شناور و چه برای سایر محصولات مهندسی شده، ایجاد شیارها در پشت پنلها است. بسته به سازنده پنل، عمق شیار متفاوت است.
اکنون پنلها به تایلهای پارکت تبدیل میشوند. اره این پنلها را به عرض برش میدهد. به طور خلاصه، در این مرحله، فرآیند ساخت پارکت مهندسی شده شبیه برش پارکتهای تمام چوب است. دستگاه سنباده با یک یا دو تسمه پارکت را از لحاظ ضخامت اندازه ای به حد مناسب میرساند. فرآیند مهمی برای اطمینان از تناسب صحیح کام و زبانه، که مرحله بعدی است. دستگاه سایدمچر نه تنها کام و زبانه را دو طرف تخته میزند، بلکه در صورت لزوم لبه را نیز مورب یا نرم میکند.
دستگاه سایدمچر
باز هم بازرسان کنترل کیفیت، برای تعیین ضخامت، پارکت را به صورت تصادفی با کولیس، کنترل میکنند. زبانهها و کامها نیز بررسی میشوند و کارگران از یک میز بزرگ برای فشار دادن تکه های پارکت به هم و بررسی تناسب و صافی آنها استفاده میکنند.
سپس دستگاه اِندمچر، کام و زبانه را در انتهای تایلها ایجاد میکند و بدین ترتیب خط تولید به فرآیندی بسیار تخصصی برای تولید پارکتهای از پیش فینیش شده تبدیل میشود. کارگران عیوب کوچک را با فیلر پر میکنند و عیوب بزرگ و کلی جهت برش برگشت میخورند و پارکت مربوطه دوباره از دستگاه اندمچر رد میشود.
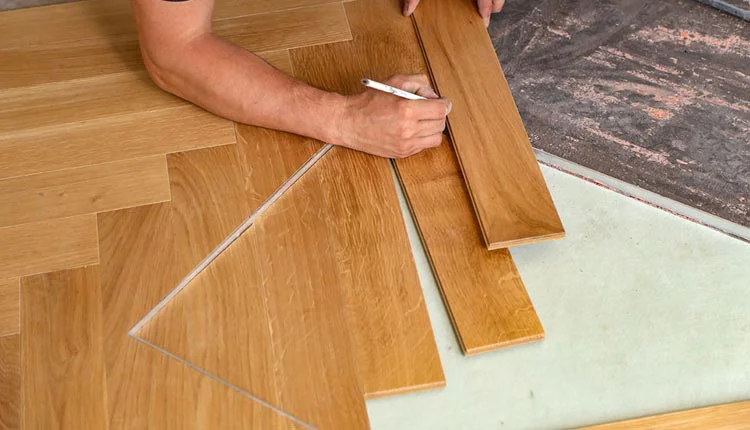
اگر انواع معایب پارکت چوبی روش حل آنها برای شما مهم است توصیه میکنیم حتما مقاله زیر را بخوانید:
البته روشهای رنگ پارکت و فینیش آن در کارخانه از کارخانه ای به کارخانه دیگر تغییر میکند. به طور کلی، این فینیش با سنباده زدن مجدد پارکت شروع می شود. سطح زیرین به آرامی سنباده میشود و سطح رویی از نمره 80 تا 220 سنباده می خورد. اگر قرار باشد پارکت رنگ شود، ابتدا با غلتک رنگ شده، سپس توسط برسهایی که در جهت مخالف میچرخند، برس میخورد. از آنجایی که باید رنگ به سرعت و کاملاً خشک شود، از اشعه ماوراء بنفش استفاده میشود.
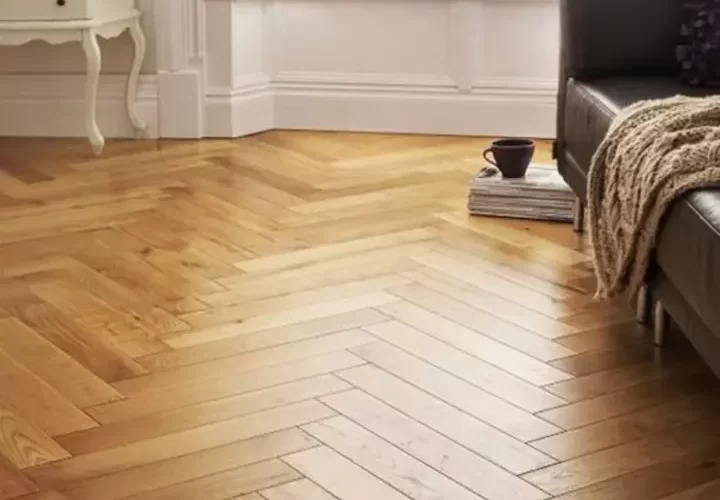
سنباده زدن پارکت و فینیش/ رنگ کردن فینیش
قبل از اعمال فینیش بادوام برای روی کار، پارکت از دستگاه «دنیبر» میگذرد- دستگاهی با سر مرتعش و مکنده که هر گونه برآمدگی، گرد و غبار یا گره های برجسته را از بین میبرد.
اکنون پارکت برای سیلرها و فینیش رویی (سطح نمایان کار) آماده است. مانند رنگ کردن، در این مرحله نیز معمولاً از غلتک استفاده شده و سپس کار در برابر اشعه ماوراء بنفش خشک میشود. در بین اولین اجرای فینیش و فینیشهای بعدی، پارکت به آرامی ساب میخورد تا چسبندگی افزایش یابد.
اکنون محصول نهایی بر اساس درجه بندیهای اختصاصی شرکت درجه بندی میشود. بهطور تصادفی، برخی محصولات از بازرسی نهایی انجام میشوند – در بین همه فاکتورها توجه زیادی به رنگ، براقیت، چسبندگی و ضخامت فینیش میشود.
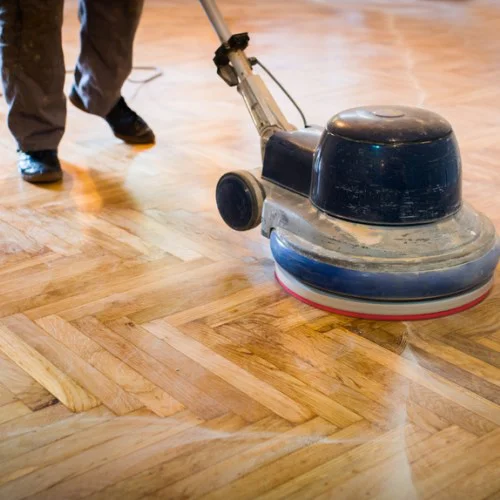
بسته بندی پارکت/ وزن کردن/ مهر و شماره زدن
برخلاف اکثر پارکتهای تمام چوب، پارکتهای با فینیش پیش ساخته بسته بندی شده و با متر مربع مشخص بسته بندی میشوند. کارتنها وزن شده تا از محتوای هر بسته اطمینان حاصل شود، و سپس مهر و شماره میشوند – این آخرین مرحله ای است که با نظارت دقیق در ساخت پارکت مهندسی شده با فینیش پیش ساخته دنبال میشود.
منبع: مورفلور
rushweb blog...
ما را در سایت rushweb blog دنبال می کنید
برچسب : نویسنده : rushweb rushweb بازدید : 118 تاريخ : چهارشنبه 2 شهريور 1401 ساعت: 13:58